Open porous ceramic foams are widely used in metal casting as filters. The foams are well suited for high temperature applications, which require managing high flow rates as well as mixing of fluids. The ceramic material and porosity of the foam can be adapted to suite individual requirements.
The demand for high performance filters has led to the development of 3d printed foam designs. These can withstand higher loads leading to less contaminations of cast products.
The high porosity and chemical resistance of ceramic foams makes them the ideal substrates for catalytic processes. With a wide variety of materials and possible coatings the catalytic converter can be adapted to match its application. Either as a monolithic converter or in bulk in a reactor.
The full potential of ceramic foams has not yet been explored since more and more applications require their unique characteristics.
Our Services
- Development and improvements of ceramic foam materials
- Phosphate-bound
- Silica-bound
- Sintered materials
- Catalytic active layers
- Rheological optimization, characterization of suspensions and slurries
- Consultation on material selection
for specific applications - Process optimizations
- Development of 3D printed foam
- Customized pores, shapes and sizes
- Manufacture of prototypes
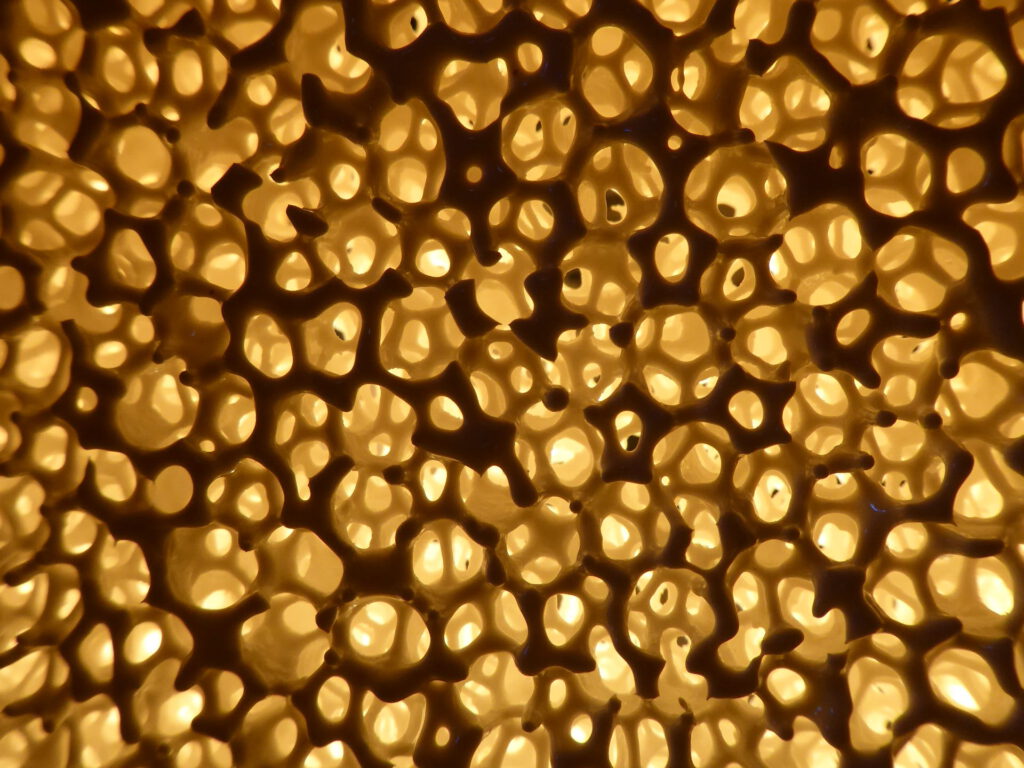
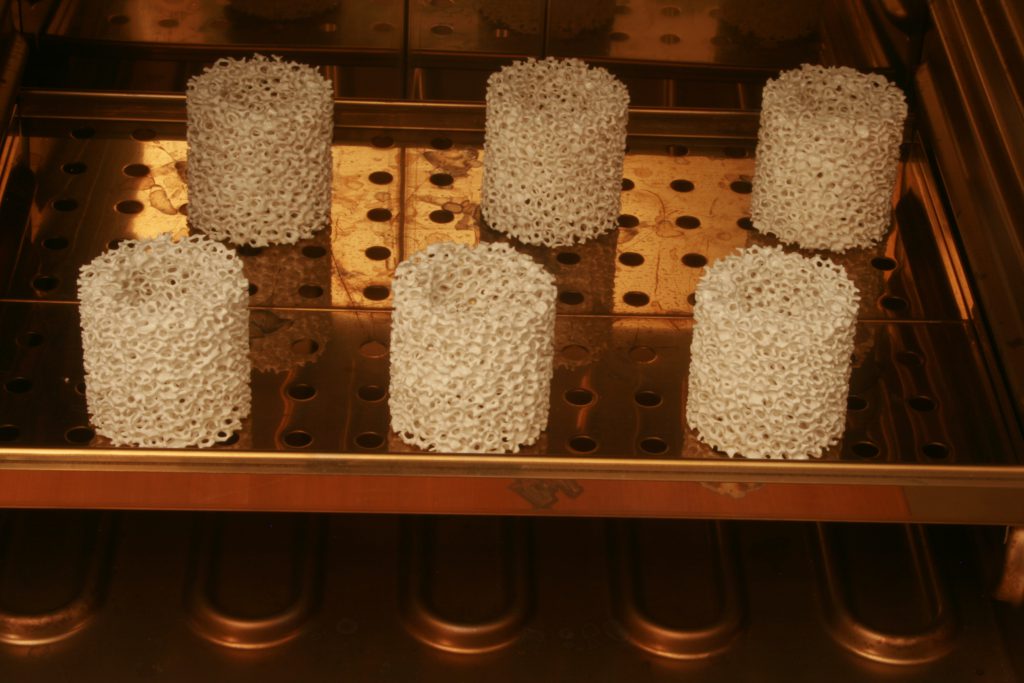
If you wish to find out more about our products and services, please contact us – we are more than happy to answer your questions!